Solar Technology Will Just Keep Getting Better: Here’s Why – Forbes
With the federal Investment Tax Credit phasing out, it’s a good time to take stock of the solar industry – both taking a look at where it has come from and where it is headed, especially in terms of innovation and evolving technology.
There are few individuals more qualified to discuss this topic than Jenya Meydbray, Founder and CEO of PVEL (PV Evaluation Labs). His company – founded in 2010 – performs independent qualification of photovoltaic solar equipment on behalf of large buyers and investors (PVEL tests both thin film and crystal silicon panels, but the vast majority of technology in the market is crystal silicon – which is where investors and developers are seeking the data).
A solar power plant is a capital-intensive venture, with an expected lifespan of as many as several decades. Operations and maintenance costs are relatively marginal, and the fuel is free, so the quality of the panels is perhaps the most critical element to consider in the overall equation.
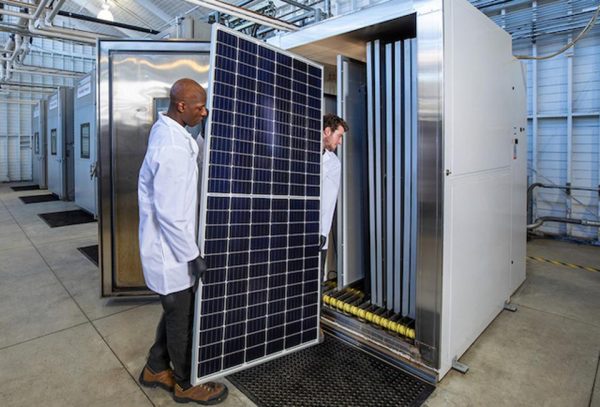
Bringing a module into an environmental chamber for accelerated testing
PVEL
As Medbray comments, “Manufacturers are selling watts, while customers are making money off kWh and those are two different things.” This dynamic becomes increasingly important with assets that must perform over a large variety of conditions and lengthy timeframe. He asks rhetorically,
Have you ever seen a plastic kid’s toy left outside for a year? Polymers and plastics degrade in the field and solar panels are no different – they have polymers and plastics. We try and make it as simple as possible to provide comprehensive solutions through our qualification program.
PVEL evaluates panels by applying sophisticated reliability and performance-testing programs to ensure the panels will perform as promised and investors can feel confident ponying up their cash. It’s no small challenge, given that the cell and panel technology continues to evolve. And the industry has already come a long way since Meydbray started.
A look back at the past decade of innovation
Meydbray comments that from an outsider’s perspective, a solar array “looks like a rectangle of crystalline solar cells glued to glass, bolted to a rack that goes through an inverter.” In that sense, he says, solar panels haven’t changed much in ten years and today they look more or less the same, “They still have 72 crystalline based cells glued to glass, bolted to a frame, and interconnected with an inverter.” However, he likens the cells to an engine in a car – an engine that has evolved greatly in the past decade, and whose costs have fallen dramatically, to perhaps 20% of what they were ten years ago.
Meydbray catalogs the items driving that trend in cost reductions, with one of the biggest levers being improved efficiencies in the manufacturing process itself. Take the utilization of silicon, for example. Although the price of silicon has plummeted from highs of $400 per kilogram to around $10/kg today, it’s still the most expensive input in a solar panel (for multi-silicon, an estimated 15-17% of total costs of goods sold). Thus, any ability to reduce the amount of silicon helps slash costs.
He cites the concept of ‘kerf loss,’ a term for the silicon lost in the sawing process during which raw silicon ingots are cut into cells. If silicon were wood, this would be the equivalent of sawdust that would go to waste. When a solar wafer – the precursor to the finished polished cell – is made – one essentially slices a giant log or brick of silicon into wafers. The widespread introduction of ultra thin diamond wire saws several years ago vastly reduces the amount of silicon lost in the process.
Meydbray observes that the cells thicknesses have stayed at about 180 microns for some time. Efforts to produce thinner cells resulted in frequent cracking during the production process, reducing overall yields. However, the widespread introduction of the diamond wire saw has recently allowed for the creation of thinner wafers (and therefore cells), though these haven’t yet moved into commercialization. He estimates the cost impact to be 1.5 cents/watt for every 10 microns of wafer thickness.
Then there is the conversion efficiency of the cell itself – how effectively it converts photons into a useful stream of electrons. This is important, since with higher efficiencies you get more watts out of the same rectangle of glass, the same frame, inverter, and labor. Since 2010, he notes, the absolute efficiency of the crystal silicon solar panel has gone up about .5% per year and “that’s pretty consistent. That’s huge. And it’s fundamental to continued cost reduction.”
One recently applied approach in this area, simply slicing cells in two (a technology referred to as ‘half cut cells’), has helped cut costs by adding five to seven watts of additional power per panel. That’s because the panel’s electrical current gets cut in half (current being proportional to the size of the cells). Since the resistive losses are proportional to the square of the current, this approach results in meaningful gains.
In general, efficiency improvements have generally come in waves and largely, but not entirely, out of China. In 2012, Meydbray comments, the first round of import tariffs was slapped on Chinese panels. These tariffs were focused on the cell – rather than the panel – level. As a consequence, Chinese manufacturers started sourcing much of their cell supply from Taiwan while continuing to assemble the panels in China. During this period, innovation slowed down considerably. PV technology was dominated by the traditional aluminum back surface field (aBSF), with little innovation until 2014, when the tariff loophole was closed and cell manufacture migrated back to China.
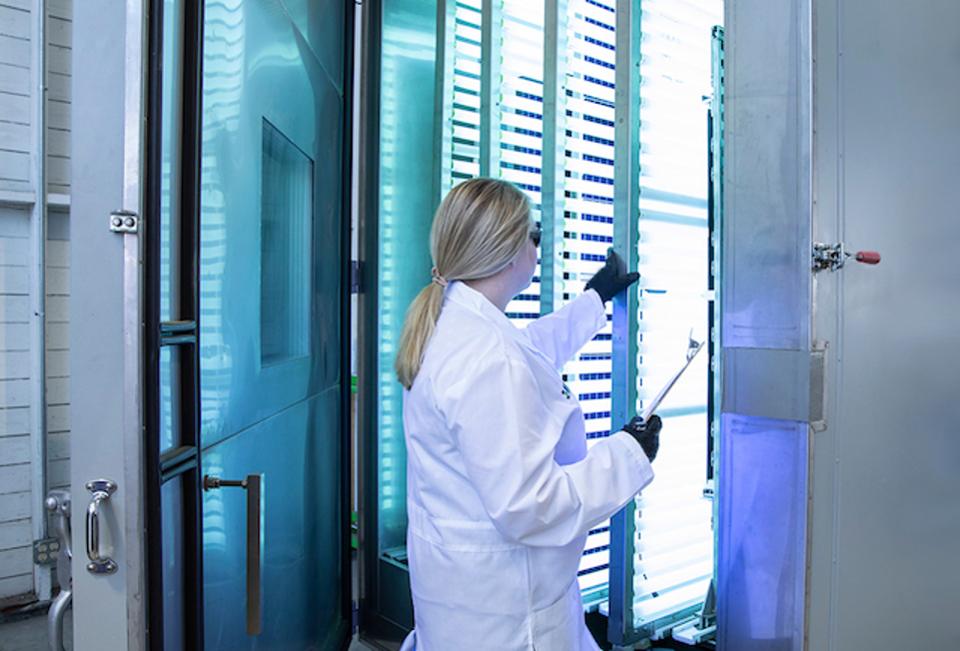
Using UV light to test backsheet durability
PVEL
With the aBSF solar cell, Meydrbray comments, one could achieve a 20% practical maximum conversion efficiency. To advance past that, it was necessary to add an additional layer to the back of the cell. Cell manufacturers began to innovate and created a new cell technology called ‘Passivated Emitter Rear Cell (PERC). The PERC technology had the advantage of reflecting previously unabsorbed light back into the cell for a second chance to convert it into electricity.
The Germany leader in making the cell manufacturing machines – Meyer Burger – figured out how to make the machines to manufacture PERC at scale, adding a “reasonably complex” additional step, he says. Soon, though, everybody figured it out, to the point that today one can now buy generic Chinese manufacturing equipment for one-third of the Meyer Burger tool and PERC has been widely adopted.
With PERC, Meydbray says, 23% cell efficiencies have been achieved, with average efficiencies at around 21.5% in the tens gigawatts of cells now being produced annually. He believes there is some efficiency runway left with PERC, but 23.5 % is probably the maximum that can be squeezed out. Meydbray also comments that the distinction between mono and polysilicon cells is not as critical as it used to be. “Within these cell technologies, you can use multi or mono cells.” Mono cells used to couple higher efficiencies with higher costs, but “At this point, mono is becoming the same cost as multi, and in some cases is even cheaper,” he says.
Meydbray indicates the solar R&D universe is now working on two technologies: heterojunction – which is a totally new cell technology (Meyer Burger is also working on this – which would necessitate a totally new greenfield solar manufacturing facility) and passivated contact “”which is incremental but difficult.” The jury is still out on both of these, but he comments “we have a few years before we need to it to go up the efficiency curve.”
And then there’s bifacial
Meydbray indicates that once the PERC cells were created, it opened up an opportunity for bi-facial panels, which are just what they sound like; symmetrical solar panels that can harvest energy from each side. The original aluminum BSF solar panels were not symmetrical, but PERC is, “so when everybody moved to PERC they were essentially manufacturing bifacial solar cells. All you had to do was take off the back sheet and you had a bifacial panel.”
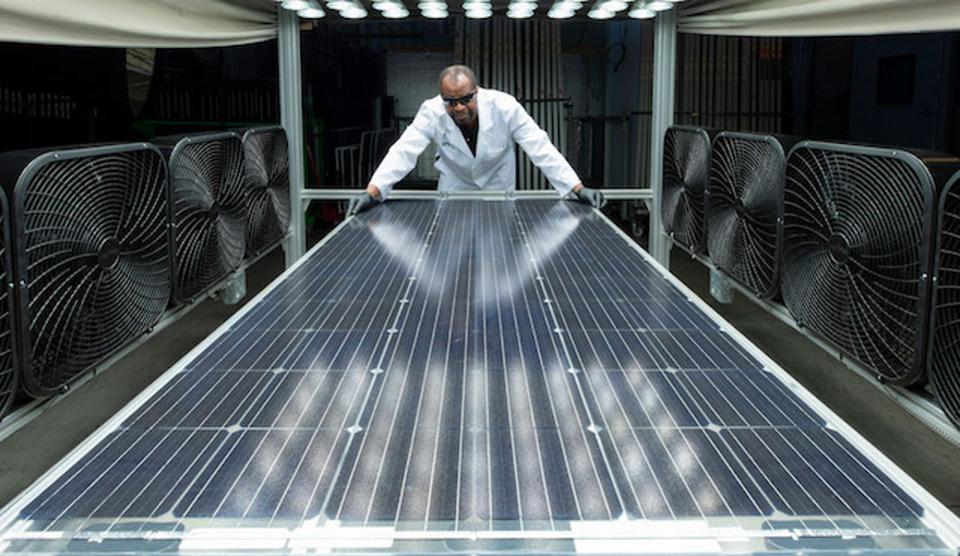
Putting bifacial capabilities to the test
PVEL
The manufacturing process for the industry giants like Jinko, Longi and others was “borderline trivial” he says, once they began making PERC cells. Clear back sheets had to be added and junction boxes (the enclosures on the module where all of the PV strings are connected that allows each module to be linked to the next) relocated to avoid blocking sunlight, but those were small obstacles.
As Meydbray explains it, the real challenge with bifacial is not in the manufacturing but in the implementation in the field, because a large number of new variables get added into the equation. To get best results from bifacial, one must maximize the amount of sunlight reflecting up to the downward facing panels. The panels must be high enough above the surface to allow maximum reflectivity, but the higher costs of steel racking affect the overall value proposition. One must also be careful to avoid having the frames block sunlight.
Placing panels higher off the ground, especially if they are on trackers that tilt the panels to follow the sun, also changes the potential wind loads to which the systems are exposed. In extreme cases, Meydbray comments, “we have had wind-related failures from trackers. They can oscillate and blow apart.” More steel can address that, but at an additional cost.
In addition, there is the issue of the mismatch between bifacial modules on edge of the system versus those in the middle that see less light on the backside. The modules are connected strings in parallel, feeding into a combiner box and inverter. Since they are in a series, they require the same current. Thus if the modules on the edge see more light than those in the middle, there is greater potential for mismatched losses.
Despite all of these various factors – and there are over a dozen to consider – Meydbray characterizes the ‘bifacial gain’ (the additional output compared with monfacial modules) as ranging from 5% to 20%,
it’s all about design conditions and cost optimization…bifacial will almost always beat monofacial economics – it’s the largest single step function improvement in levelized costs of electric since the introduction of trackers.
Meanwhile, other improvements are being made across the spectrum
The cells themselves have been increasing in size. What used to be a standard 156.75 millimeters (mm) cell was initially increased to 158 mm, and Meydbray indicates that cells are now moving to 161 mm. Longi – The world’s biggest monocrystalline silicon module maker, with plans to produce 30,000 MW of modules by 2021– recently announced a move to 166 mm, with plans to switch its entire production over by 2020.
The growth is relatively incremental, he says, “moving by one, two, three, or four millimeters…Somebody realized solar cell manufacturing equipment could fit a slightly larger cell” with the result that manufacturing costs fall on a per watt basis. When you get to 166 mm, though, it’s sufficiently bigger that you need incrementally different designs in the cell manufacturing equipment.
Meydbray cautions that with every incremental incremental design change “there are implications that are often overlooked until you have failure” or at least significant challenges. For example, if one makes the cells bigger, without changing the number of cells in the panel, then the panel is no longer backwards-compatible. This means that a new and slightly larger panel cannot be retrofitted into an existing field if older panels malfunction. Or in the case of systems with trackers, a slightly higher panel might increase the torque forces from the wind, which are proportional to square of height of the panel. As a result, one must either risk failures or invest in incrementally more expensive racking structures. In that sense, everything is an interconnected ecosystem.
Solar is a game of shaving pennies. Other incremental improvements are also taking place, further driving down costs or increasing efficiencies. Take busbars – the thin flat wires that collect the current created by the cells and connect each cell to the next, ultimately delivering power to the inverter, that in turn sends it along to the grid. These busbars, Meydbray says, are somewhat like the blades in razors. From an initial starting point of two busbars on a cell, there are now typically five, which increase redundancy in the event of failures. Meanwhile, the busbar widths have been reduced to minimize overall cell shading losses. The next step here is changing the interconnection design altogether, “so that we are now up to 12 busbars that are extremely thin. Meyer Burger is currently making a metal grid with 30, 40, or 50 wires they call smart wire, which will create further optimization in the cell interconnect.”
Meydbray points to another emerging approach called shingling. In the panel with its individual cells, there is space between each cell, where light is not hitting active solar material. With shingling, the cell is cut into five or six strips and overlaid like shingles on rooftop, “so you have complete coverage of the real estate of the solar panel…It’s now on everybody’s technology road map.” And it can be undertaken with both PERC and aluminum BSF technologies.
There are also other tiny adjustments that add up, such as a tape from 3M that addresses the light that reflects off the busbars. This thin tape redirects light at an angle so it reflects off the glass and gets reabsorbed by the cell, squeezing more efficiency out of the panel.
And finally, there are anti-soiling coatings being developed to minimize losses that occur when panels are compromised – as much as 30% or more – by layers of particulates from air pollution, or dust from weather or agricultural activities. Washing panels is expensive, “A crew with hose spraying down panels is on the order of 25 cents per solar panel for a large site,” he notes, so a coating that minimizes the need for cleaning helps further lower costs and improve efficiencies.
The bottom line, Meydbray summarizes, is that “there has been a ton of technological innovation over the last decade and its not slowing down. It’s continuing on the same trajectory.” And as costs continue to fall, he predicts, more markets will continue to open up.
There is always the next horizon. Solar was adopted first in places where electricity costs are high and it’s sunny. Then as costs fall, there is always the next market where it’s cheaper than the conventional incumbent.